15 August 2019
Image: Bonnie Doon House | By Archiblox < < click me to see more
Modular Mode
Is the Future of Prefab Construction Modular?
Original Article by: Chris Knierim for Grand Designs Australia. Read full Article In Grand Designs Magazine.
Prefabrication of parts and off-site construction modules has been a practice for more than 10 years. However, in the last couple of years, we’ve seen changes in the industry move towards bringing the work in-house.
La Trobe Tower in Melbourne, with 44 storeys and standing at 133m, is now officially Australia’s tallest prefabricated building. The residential tow was constructed in only 16 months. Similar projects are going on in the UK and the US.
The experts behind all these projects share the same vision: the future is modular. They believe the technology needed to have modular construction finally exists and they plan to show it. The problem is that many people still don’t believe in this way of building, even though, since the 1990’s, government reports were saying that modular construction is safer and faster, while not compromising on quality of the construction.
Interested to know more? Start a conversation with us.


Images: Avalon Light Impact Beach house | By Archiblox < < click me to see more
Unfortunately, the majority of buildings worldwide are still made the old-fashioned way – on site. What keeps the hope of having a modular future alive is many large-scale projects around the world that are built using this technology. Projects such as Google Headquarters, which was designed by Bjarke Ingels; Creekside Wharf in Greenwich, which is the tallest modular structure in the UK; and the La Trobe Tower, which is the highest in Australia.
The benefits of modular construction are many. It is a safer way of building but at the same time it can be both cheaper and faster. Contractors are now able to start working on foundations on-site and start with the manufacturing process in the factory. Experts have calculated this can enable projects to be finished up to 50 per cent faster than traditional construction.
Furthermore, modular construction and prefabrication lowers the amount of material waste, plus it allows constructors to continue production even in bad weather. This type of development also enables us to rethink the use of buildings since, in the future, modular structures could be disassembled and shipped to other locations for reuse.
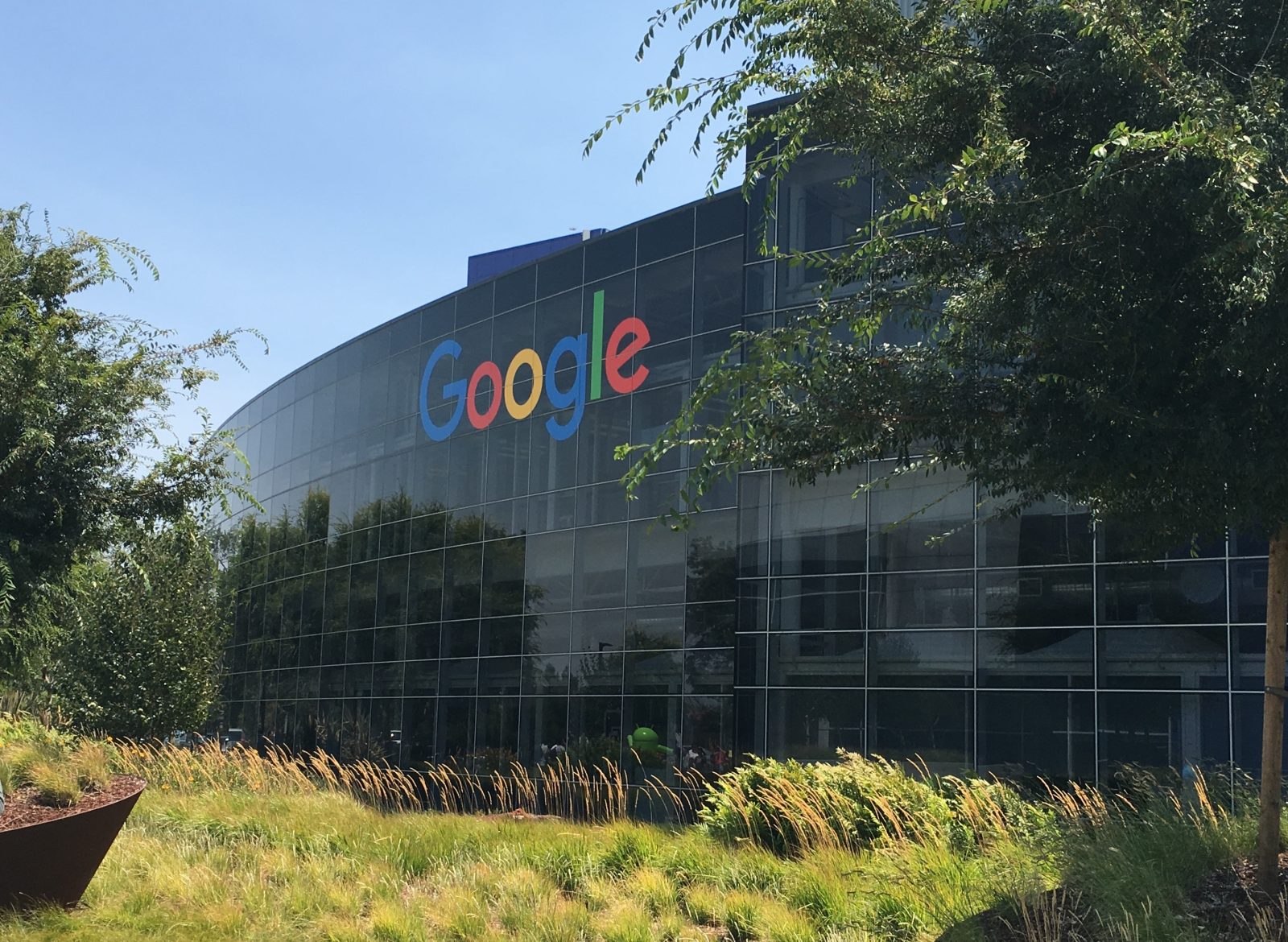
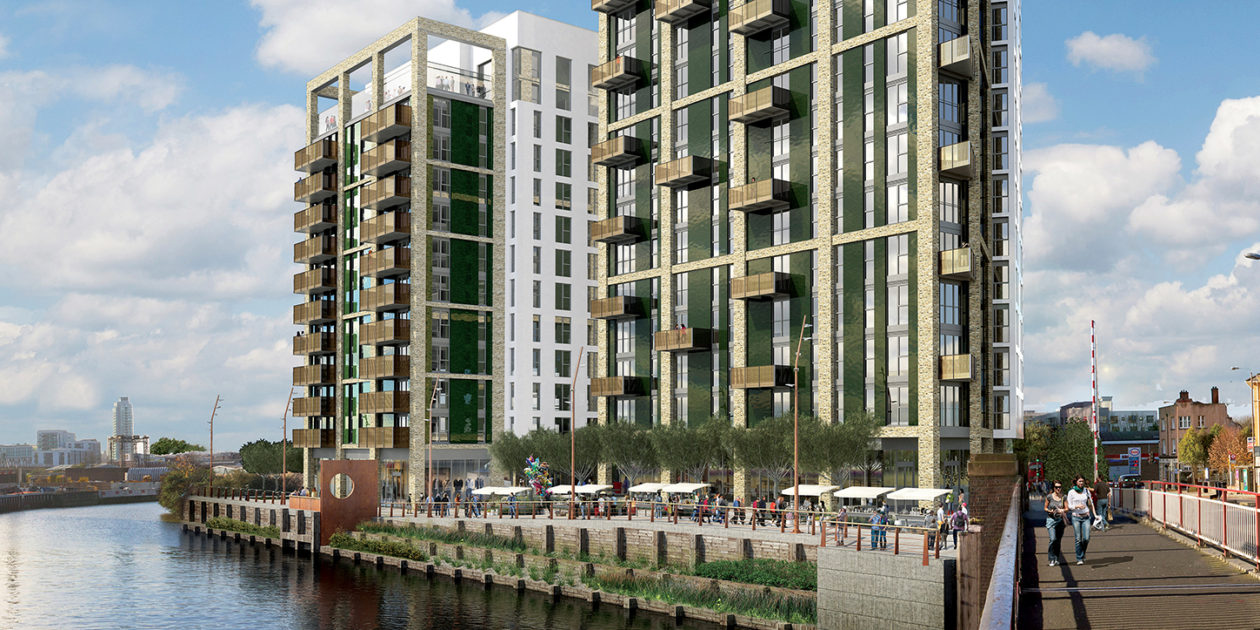
Images: Google Headquarters, USA + Creekside Wharf, Greenwich, UK
The experts find modular construction to be excellent when it comes to managing quality. Whatever is manufactured on-site can vary in quality, especially when the builder doesn’t have strict quality control. However, when you produce something in a factory, it is easier to establish control over quality and make sure that every single modular piece is up to standard.
On the other hand, the builder will have to worry about the transport of modular elements from the factory to the construction site. Tolerances would have to be higher in the factory since every module needs to be shipped.
So, what’s slowing down the adoption of modular construction? The benefits are apparent but it’s still far from everyday use. Experts agree there are many reasons for this, most of them being economical, technical and financial.

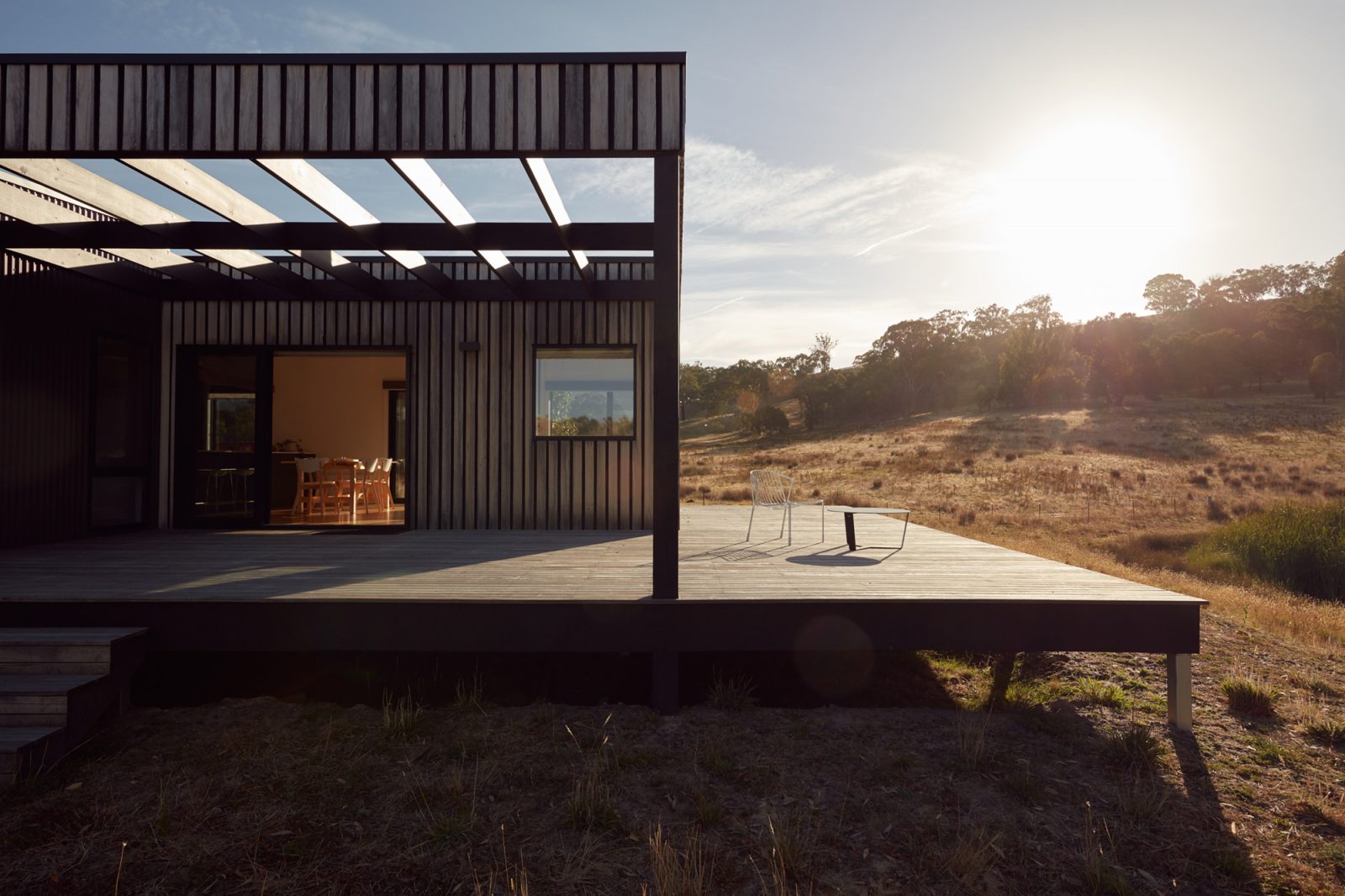
Image: Bonnie Doon House | By Archiblox < < click me to see more
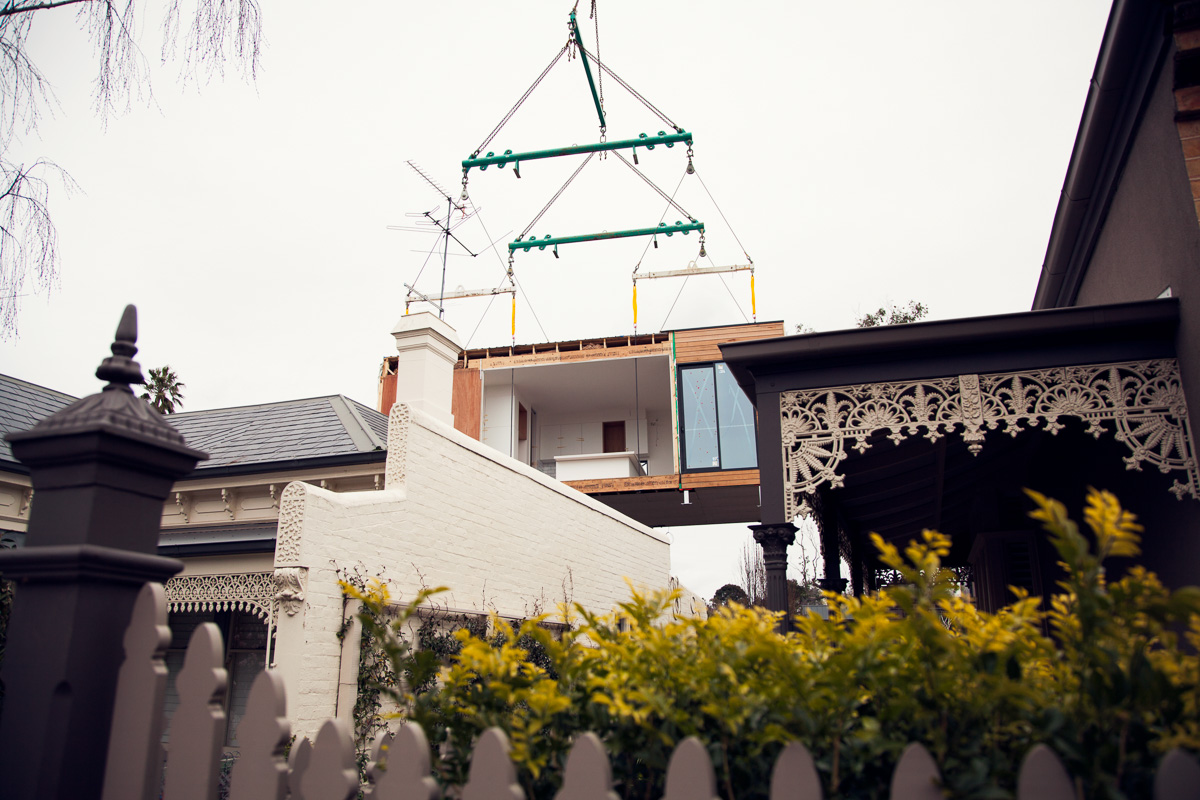
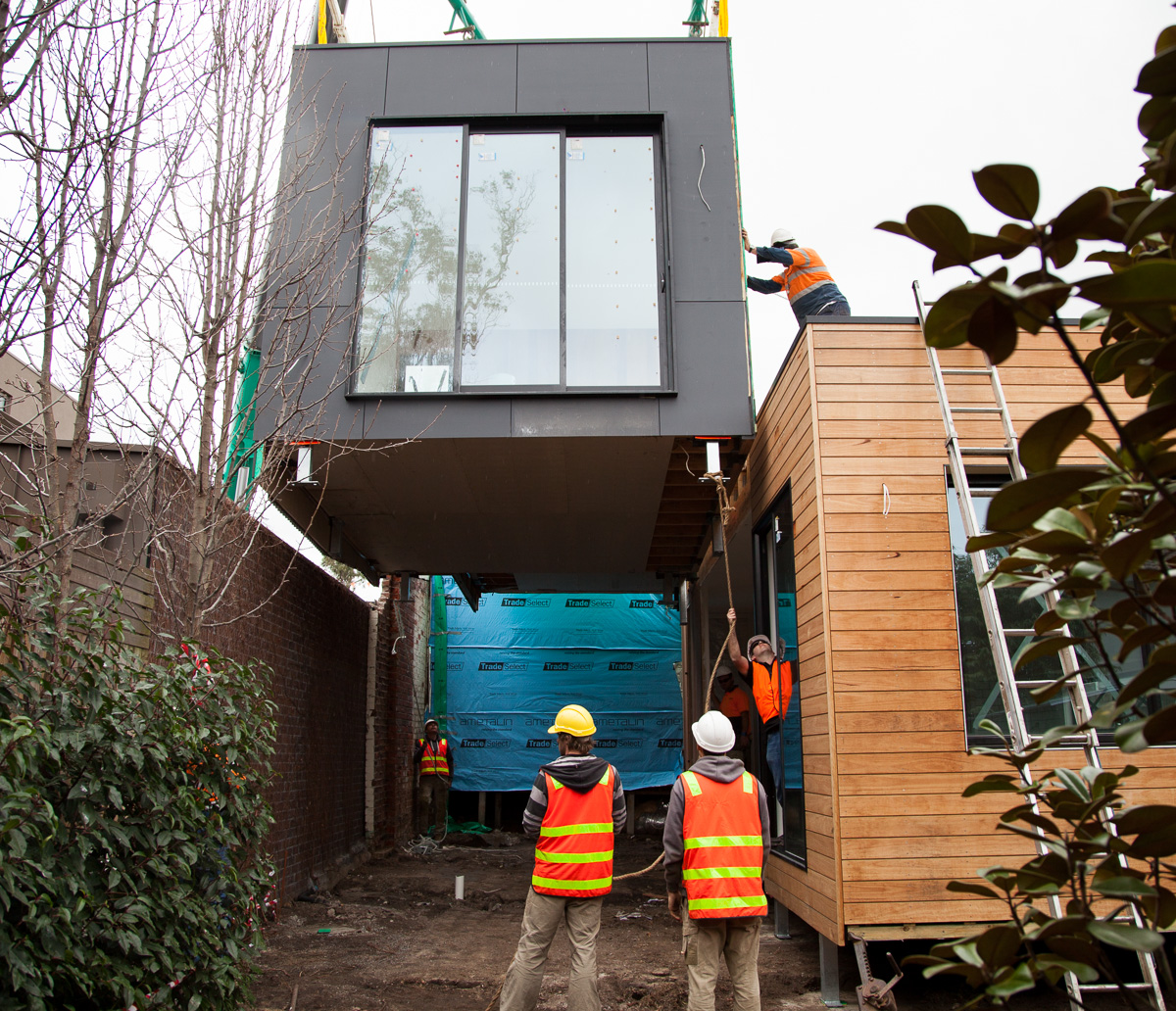

Images: Hawthorn Extension | By Archiblox < < click me to see more
Think Outside the Box
A great example of modern prefabrication being used in construction is the Crowne Plaza Hotel extension at Changi Airport. Singapore’s construction regulator stated that at least 65 per cent of tower superstructures must use PPMC (prefabricated pre-finished modular construction). The PPMC helped lower the number of workers required on-site by 40 per cent. Furthermore, the construction of one floor took three to four days, instead of two to three weeks.
Designers have been interested in modular construction for a long time. They are fascinated by the possibility of adding new modules where needed, or for their structures to be able to adapt to ever-changing urban environments.
It all points to the construction industry of the future being modular. As the robot technology develops, one day it will enable fast and accurate production of prefabricated modules. As the manufacturers and designers around the world are getting familiar with the technology, we might see some new and exciting structures being built.
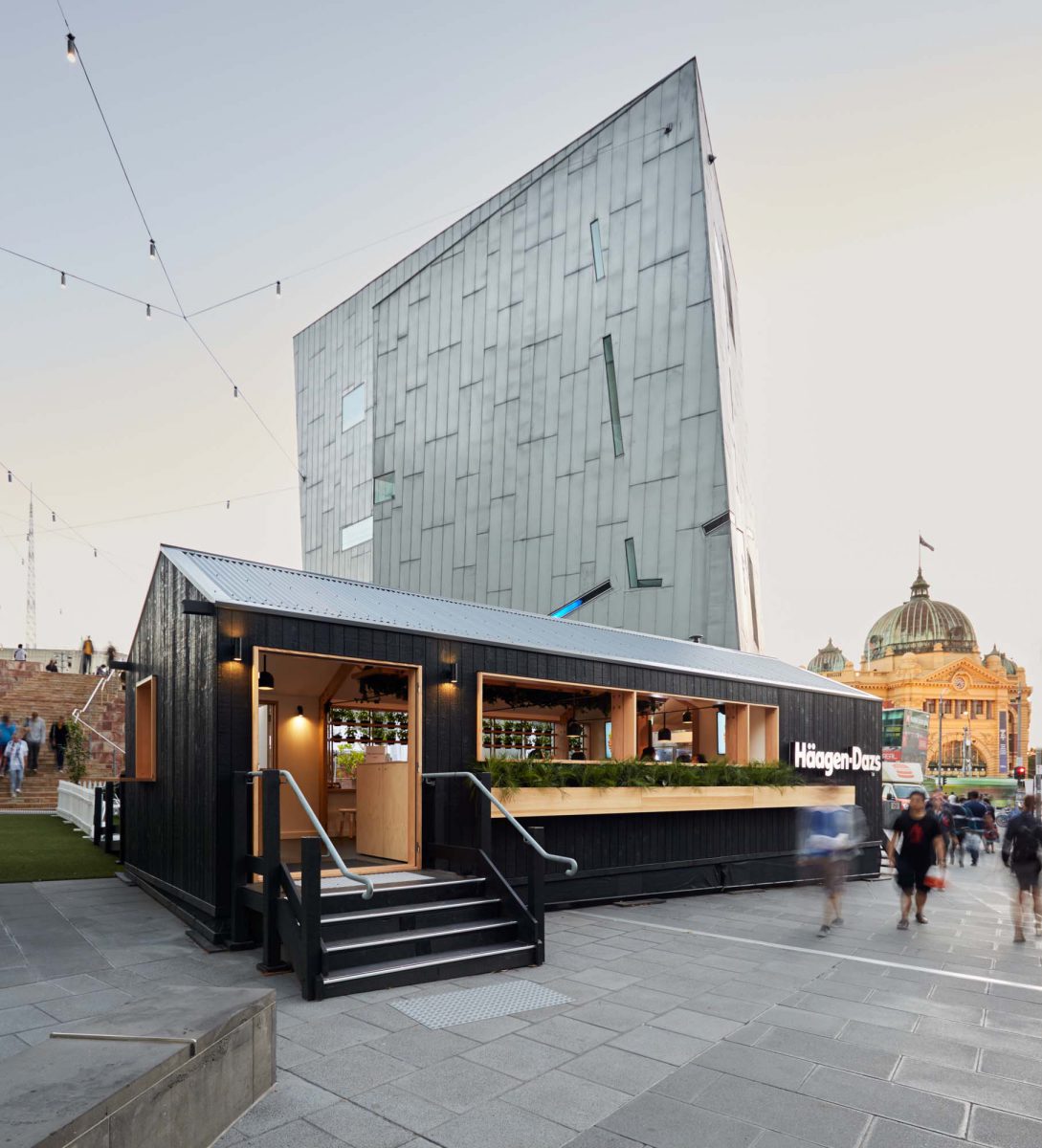
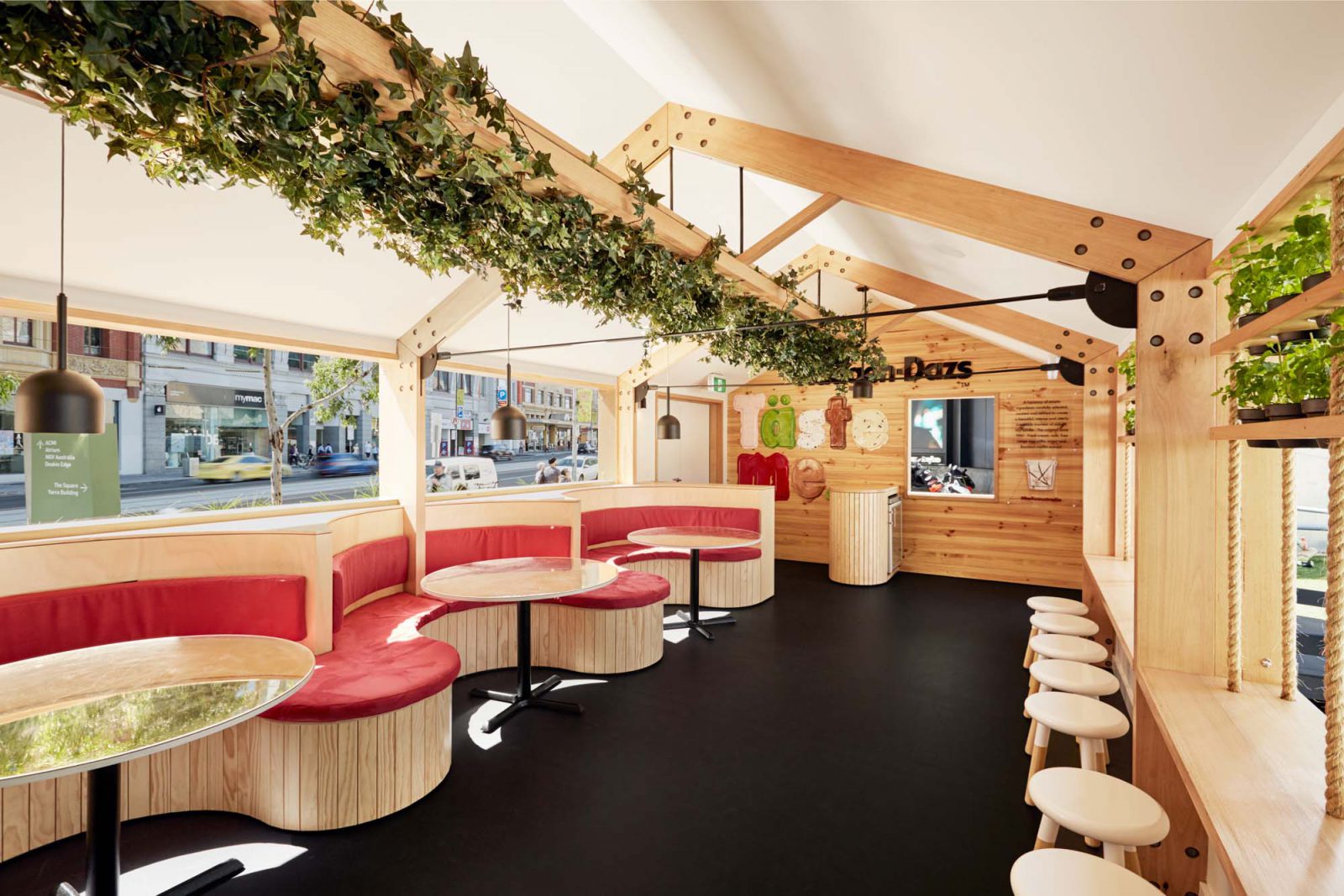
Images: Haagen Dazs | By Archiblox < < click me to see more
The market is always looking for novel and cheaper ways to build. In a world where there aren’t enough skilled workers, modular might be the way to go.
Designers and manufacturers are slowly embracing the idea and with the current lack of skilled workers available to carry out traditional house builds, prefab buildings might just be the solution.
Chris Knierim is an international award-winning designer and builder. He is the national president of the Building Association of Australia and sits on the board of the Australian Design Alliance.
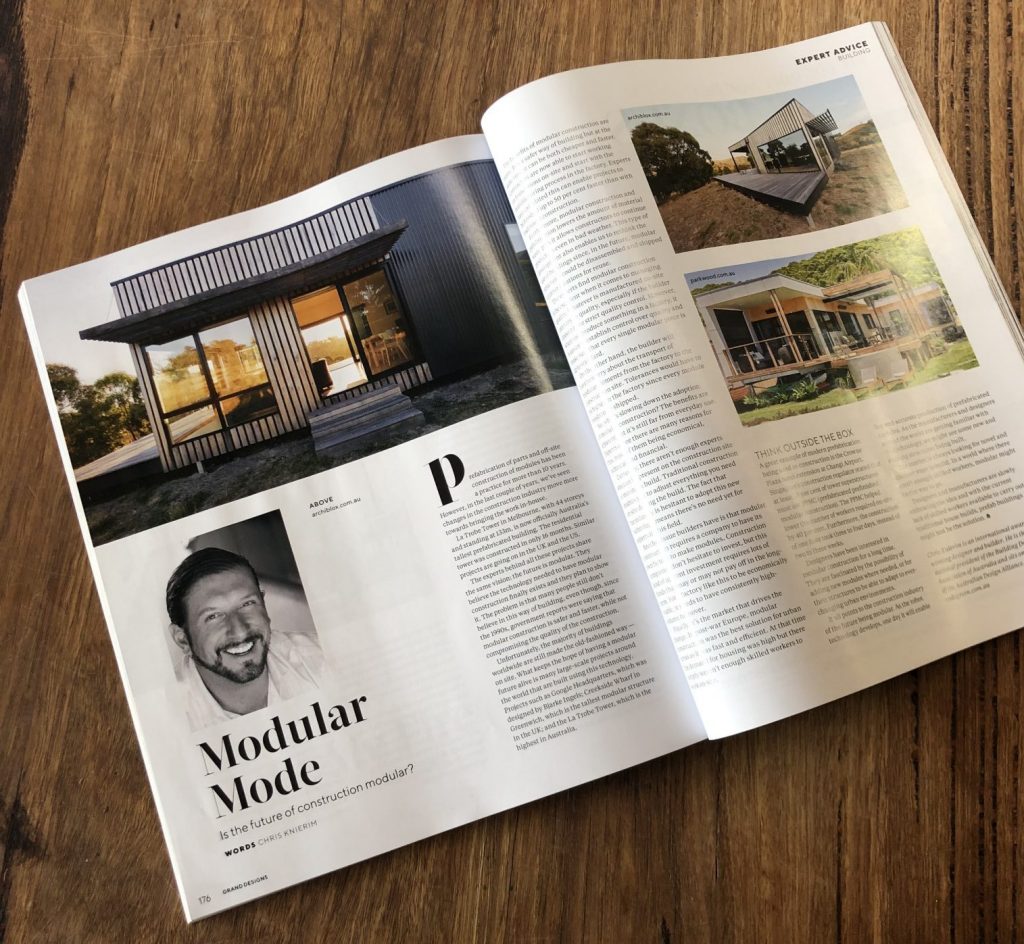
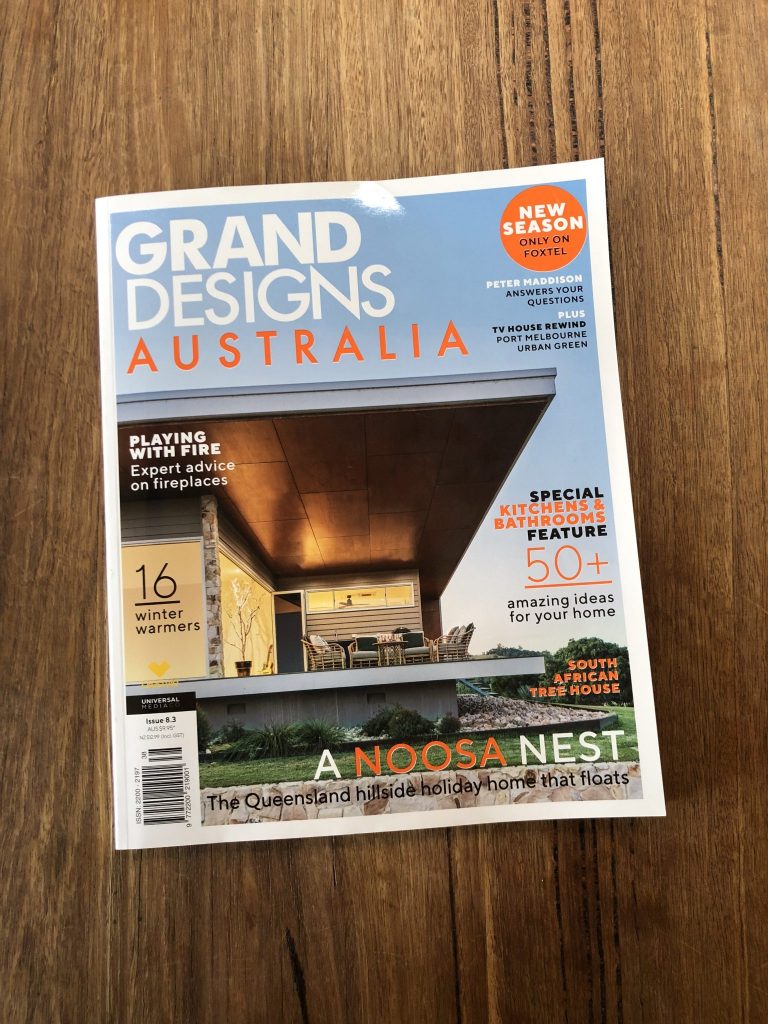
Check out our Smart Prefab Homes < < click here. For more information on Modular Design & Construction < < please click here to get in touch, we'd love to hear from you.
We love sharing all the new and exciting things happening at Archiblox, so make sure you’re following us on Instagram, Facebook and
Twitter, or signed up to our monthly newsletter, to ensure you don’t miss a thing.